Comprehending the Importance of Timely Stretch Cover Device Fixing Solutions
When it concerns extend cover devices, prompt repair work can make all the distinction. You know that even small mechanical or electric issues can result in unanticipated downtime, impacting your assembly line. Resolving these troubles rapidly not just maintains efficiency however additionally improves the high quality of your covered products. So, what aspects should you consider to ensure your devices remain in top form? Let's explore this important facet better.
The Duty of Stretch Wrap Machines in Modern Production
Stretch wrap machines play a crucial role in modern production by ensuring that products are securely packaged for transport and storage space. You count on these equipments to offer stability and protection, protecting against damages throughout transit. When you use stretch wrap, you reduce the danger of items changing or obtaining crushed, which can lead to costly losses.
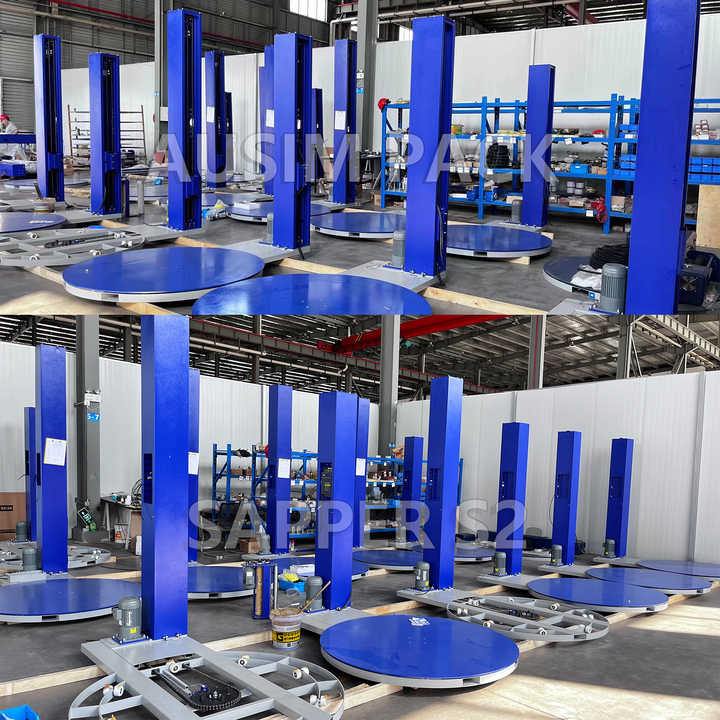
Moreover, making use of stretch cover devices can enhance your total supply chain performance. By simplifying the product packaging procedure, you reduce labor costs and accelerate delivery times, guaranteeing that your customers receive their items immediately. In today's busy market, this benefit is vital.
Common Issues That Bring About Maker Downtime
When your stretch wrap device experiences downtime, it can frequently be mapped back to mechanical failures or driver errors. Recognizing these common concerns can help you avoid expensive disturbances. By resolving these factors, you can keep your procedures running smoothly.
Mechanical Failings and Break Downs
When components put on down or break, your stretch cover machine may stop suddenly, influencing productivity. In addition, electric failures can trigger breakdowns in the equipment's control system, creating further hold-ups. By prioritizing prompt fixings, you're not just decreasing downtime however likewise extending the life expectancy of your equipment.
Driver Mistakes and Oversights
While operators play a vital role in the smooth functioning of your stretch cover maker, their errors and oversights can result in substantial downtime. Usual problems like improper loading, incorrect settings, and failing to monitor wrap tension can trigger hold-ups and product damages. If an operator disregards to inspect for worn-out film, it can lead to inconsistent wrapping and boosted waste. Furthermore, miscommunication throughout shifts can cause essential changes being ignored. It is essential to supply extensive training and routine refreshers to lessen these blunders. Encouraging a culture of responsibility and watchfulness among your team can substantially reduce downtime. Inevitably, purchasing operator training settles by boosting performance and prolonging your equipment's life expectancy.
The Financial Impact of Postponed Repair Work
Delaying fixings on your stretch cover maker can lead to substantial financial consequences that ripple through your whole operation. When your equipment breaks down, productivity plummets.
Furthermore, long term hold-ups can intensify minor issues into significant problems, calling for extra comprehensive repairs or even full substitute of the maker. This can strain your spending plan and interrupt money circulation. Hold-ups can likewise influence your delivery timetables, harming client satisfaction and possibly creating you to lose company to competitors. Inevitably, timely fixings are necessary to keeping your profits and ensuring smooth procedures. Don't take too lightly the financial effect of overlooking those repair requires.
Advantages of Proactive Maintenance Programs
Prompt fixings can conserve you from pricey downtime, but implementing a proactive upkeep program takes it an action further. By on a regular basis scheduling maintenance, you can identify possible problems prior to they escalate into significant troubles. This not just keeps your stretch wrap device running smoothly however additionally prolongs its lifespan. You'll locate that consistent maintenance lowers the likelihood of unanticipated malfunctions, enabling your operations to run much more efficiently.
In addition, a positive approach boosts efficiency. With less interruptions, your workforce can concentrate on their jobs without the stress and anxiety of unexpected device failings. Plus, you'll likely reduce repair service prices, as minor problems are generally less costly to deal with than substantial repairs. Preserving peak efficiency can boost the quality of your wrapped items, making sure consumer satisfaction. In the future, a positive maintenance program is a financial investment that pays off via increased integrity and price financial savings.
Determining Indications That Your Equipment Needs Repair
As you operate your stretch wrap machine, it is vital to remain cautious for indications that suggest it may require repair work. If the film isn't adhered properly or you see irregular stress, your maker may be malfunctioning.
Another indicator is an increase in downtime. If your device often stops or needs modifications, it Read Full Article is time to examine. Also, keep an eye on the equipment's speed; if it's slower than usual, something could be incorrect. Any type of visible damages like frayed wires or leaks need to not be neglected. Quickly resolving these indicators can protect against extra considerable problems down the line, guaranteeing your operations run efficiently.
Choosing the Right Fixing Service for Your Requirements
Just how do you select the right repair solution for your stretch wrap equipment? Consider their experience and competence. Look for professionals who concentrate on Visit This Link stretch wrap machines and have a tried and tested performance history. Inspect online reviews and testimonies to determine consumer satisfaction.
Following, examine their feedback time. A dependable service ought to provide timely assistance, as equipment downtime can be pricey. It's additionally important to understand if they supply emergency situation fixings.
Do not forget to inquire about warranties on repair work and parts. A trustworthy service guarantees their work, offering you peace of mind.
Finally, compare pricing but avoid choosing solely based upon expense. Often, the most affordable alternative might cause poor solution. By considering these factors, you'll locate a repair work solution that fulfills your needs and keeps your stretch wrap device running efficiently.
Methods for Lessening Stretch Cover Maker Downtime

Educating your operators is an additional crucial method. Equip them with the understanding to identify and resolve small problems prior to they result in considerable failures. Encourage them to keep a log of any type of abnormalities, which assists in detecting concerns much faster.
Furthermore, preserving a supply of crucial spare parts can dramatically decrease downtime. When something breaks, having the right parts available indicates you won't have to wait on deliveries.
Last but not least, consider spending in real-time surveillance systems. These systems can signal you to efficiency changes, enabling immediate intervention. By applying these approaches, you'll keep your stretch wrap machine running efficiently and efficiently.
Often Asked Concerns
Just How Typically Should Stretch Wrap Machines Be Serviced?
You should service stretch wrap machines routinely, preferably every 6 months. If you see any efficiency problems or uncommon sounds, do not wait-- routine maintenance right away to stop pricey break downs and guarantee peak performance.
What Are the Normal Costs Related To Stretch Wrap Maker Fixes?
Common expenses for stretch wrap equipment repair work vary, but you might expect to invest in between $200 to $1,500 depending on the issue. Normal upkeep can aid lessen these costs and extend your machine's lifespan.
Can I Carry Out Basic Upkeep on My Stretch Wrap Equipment?
Yes, you can do basic upkeep on your stretch cover machine. Regularly examine for deterioration, clean the components, and guarantee correct lubrication. Keeping it in good form can prolong its life expectancy and improve performance.
How Do I Know if a Repair Service Service Is Credible?
To locate a trustworthy repair solution, inspect on the internet testimonials, request referrals, and validate qualifications. A reputable solution will offer clear quotes, guarantee options, and prompt communication, ensuring you feel great in their experience.
What Should I Carry out in Case of an Emergency Situation Maker Failure?
In case of an emergency machine failure, you ought to right away stop operations, analyze the problem, and contact your repair service. Keep important get in touch with numbers useful, and record the issue for reliable fixing when aid gets here.
Verdict
To sum up, understanding the significance of timely stretch wrap machine fixings can substantially boost your operations. By resolving issues promptly, you reduce downtime and avoid costly failures. Welcoming aggressive upkeep not only extends your equipment's life-span yet also boosts performance and consumer fulfillment. Keep in mind to stay watchful for signs of wear and pick a trustworthy repair service to keep your image source machines running efficiently. Investing in these services repays over time, ensuring your supply chain remains reliable and efficient.